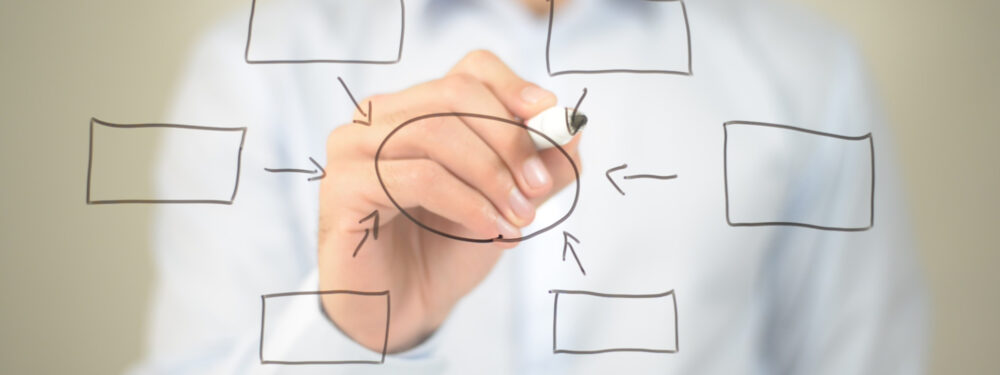
Картирование потока создания ценности (Value stream mapping, VSM) — это один из инструментов, позволяющих компаниям выявлять производственные потери и повышать эффективность за счет визуализации, анализа и рационализации рабочих процессов. Данная методика активно применялась с 1950-х годов на заводах компании Toyota. Со временем ее стали использовать для оптимизации бизнес-процессов в логистике, IT-сфере, сервисных компаниях, медицинских учреждениях и других областях. Что представляет собой карта потока создания ценности и как ее разработать — читайте в нашем материале.
Карта потока создания ценности: структура, элементы и преимущества инструмента
Карта потока создания ценности — это инструмент визуализации и анализа бизнес-процессов компании, позволяющий в формате блок-схемы выстроить всю цепочку создания продукта — от закупки сырья до поставки конечному потребителю. Главная цель метода — устранение элементов производственного процесса, которые не добавляют продукции ценность.
VSM состоит из трех основных компонентов:
- Информационный поток — отражает движение информации, управляющей ходом производства изделия или услуги. Обозначается вверху схемы.
- Материальный поток — показывает производственный процесс, фактическое перемещение сырья и готовых изделий между этапами производства. Изображается в центре карты.
- Временной поток — визуализирует временные затраты на каждую операцию. Отмечается в нижней части схемы с помощью двухуровневой шкалы: время, которое создает ценность, и время, не создающее добавленной стоимости.
Для составления VSM используется набор условных обозначений, разделенных на четыре категории: процесс, материал, информация и общие.
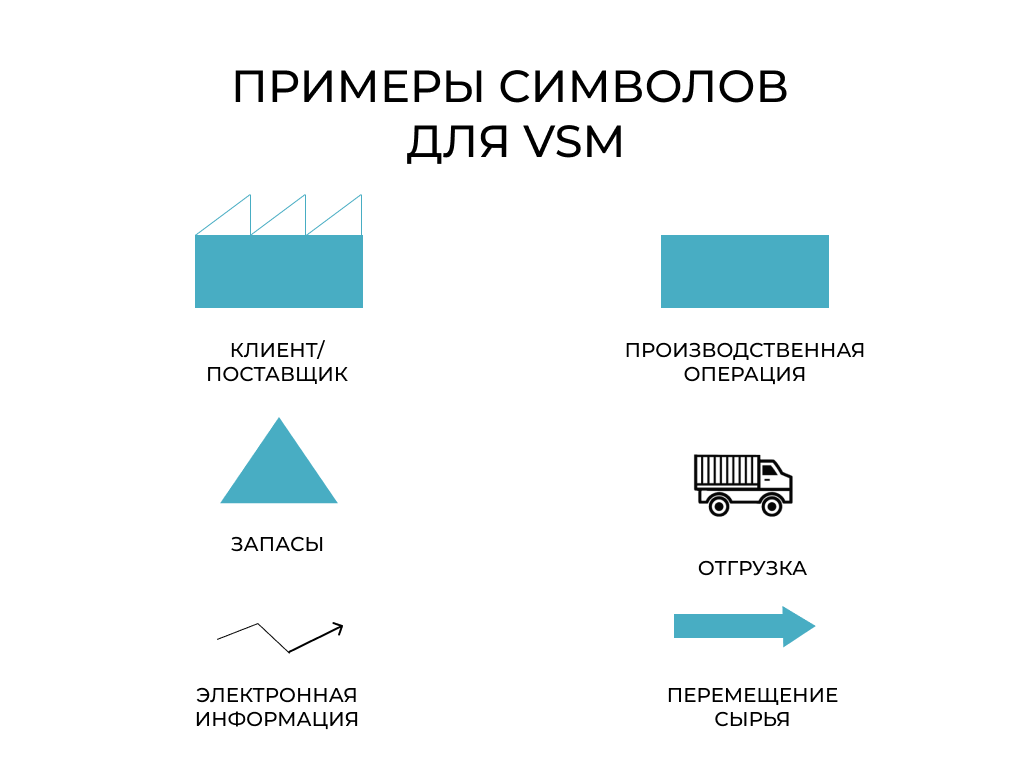
Преимущества использования инструмента:
- Выявление потерь и неэффективных операций. Благодаря VSM можно четко увидеть, где в процессе возникают задержки, брак, лишние этапы. Это позволяет сконцентрировать усилия на оптимизации проблемных зон.
- Сокращение времени производственного цикла. Устранение неэффективных операций позволяет существенно ускорить процесс производства и движения продукта к потребителю.
- Снижение запасов и затрат на хранение. VSM наглядно демонстрирует, где в процессе образуются лишние запасы продукции и сырья. Оптимизация этих участков снижает потребность в резервах.
- Улучшение взаимодействия между подразделениями. VSM охватывает весь производственный процесс от начала до конца, что позволяет наладить эффективное взаимодействие между подразделениями.
- Вовлечение персонала в оптимизацию. При построении VSM сотрудники самостоятельно анализируют свои участки работы и предлагают идеи по улучшению. Это повышает их мотивацию.
- Визуализация процесса. VSM наглядно демонстрирует, как протекает процесс в целом и на отдельных этапах. Это упрощает изучение ситуации и поиск вариантов по улучшению.
Этапы создания VSM
Чтобы сформировать практичную карту потока создания ценности, нужно пройти шесть последовательных этапов.
Этап 1. Выбор потока для анализа. На первом этапе необходимо определить конкретный продукт, работы или услуги, процесс по созданию которых будет проанализирован.
Картирование всех производственных и вспомогательных процессов на предприятии — трудоемкая задача, которая потребует больших временных и человеческих ресурсов, поэтому лучше определить конкретный поток.
Существует два основных подхода к выбору объектов анализа:
- Определить наиболее массовые, высокооборотные продукты. В этом случае выявленные потери будут наиболее масштабными и значимыми для оптимизации.
- Сфокусироваться на наиболее проблемных, «узких» продуктах, именно при их производстве потери наиболее выражены.
Этап 2. Разработка шаблонов описания объектов. На втором этапе команда должна определиться с тем, какую информацию необходимо собрать для создания карты потока ценности.
Один из обязательных объектов картирования — операция, которая обозначается на карте прямоугольником. В шаблоне фиксируется ее название, а также ряд необходимых аналитических показателей:
- количество операторов,
- время операции,
- время цикла,
- размер брака,
- общая эффективность оборудования,
- доступное время на выполнение операции и прочее.
Аналогичные шаблоны разрабатываются для фиксации промежуточных состояний процесса: ожидания, перемещения людей, транспортировки, погрузочно-разгрузочных работ. Команда договаривается о том, как описывать документооборот (бумажный или электронный), проблемы (их чаще всего изображают в виде вспышки), способы транспортировки и хранения, методы перемещения и так далее.
Полученная информация позволит в дальнейшем выявить различные виды потерь.
Этап 3. Подготовка базовой карты потока. На третьем этапе создается базовая карта — схема, отражающая общую логику и последовательность процессов создания продукта или услуги. Это своего рода каркас будущей VSM, не содержащий фактических данных.
Удобнее всего сначала построить базовую карту вручную — на ватмане, с использованием стикеров для обозначения этапов и стрелок для связей. Это позволит легко корректировать схему. Затем ее можно перевести в электронный формат.
Главный результат этапа — четкое понимание хода процесса и точек сбора данных для последующего анализа с помощью инструмента VSM.
Этап 4. Сбор данных путем наблюдения. На четвертом этапе происходит сбор сведений о характеристиках текущей конфигурации процесса создания потребительской ценности. Для этого проектная команда проводит наблюдения за рабочими постами всей производственной цепочки.
Чем больше будет проведено замеров полных циклов производства продукта или услуги, тем точнее и информативнее получится VSM. Рекомендуется сделать минимум семь замеров.
Вся информация фиксируется в подготовленные ранее унифицированные формы, что облегчает дальнейшую обработку. Это могут быть чек-листы, таблицы или иные структурированные документы.
Этап 5. Внесение данных в карту потока ценности и анализ. На пятом этапе собранные в ходе наблюдения данные вносятся в карту потока ценности.
Ключевым моментом является нанесение на шкалу времени показателей длительности отдельных операций и состояний, а также разделение их на элементы, создающие и не создающие ценность для клиента.
Далее проводится углубленный анализ потока создания ценности:
- общее время производственного цикла, время такта и время цикла;
- рассчитывается коэффициент эффективности потока;
- оценивается общая производительность;
- выявляются потери и «узкие места».
В итоге получается информативная карта с наглядными данными о текущем состоянии процесса создания продукта/услуги.
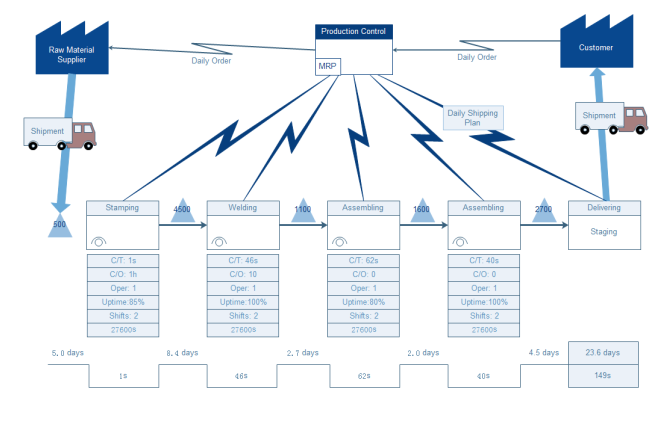
Этап 6. Построение целевой карты будущего состояния процесса. На заключительном, седьмом этапе создания VSM формируется целевая карта — модель оптимального состояния производственного потока.
Целевая VSM позволяет четко сформулировать систему KPI и метрик, а также наглядно донести концепцию оптимизации до всех участников процесса. Реализация данной модели требует соответствующего плана преобразований с привязкой к конкретным мероприятиям, срокам и ответственным лицам.
На что следует обратить внимание?
- Сформулируйте цель. Перед тем, как приступать к подготовке карты, определите конкретную проблему, которую требуется решить с помощью VSM — нехватка товарных запасов, нарушение сроков поставок, высокий процент брака. Без четкого понимания цели карта может получиться абстрактной и не иметь практического применения.
- Соберите рабочую группу. Пригласите в нее сотрудников всех отделов, связанных с оптимизируемым процессом. Кросс-функциональная команда обладает необходимыми знаниями, опытом и взглядами на разные части общего процесса, что важно для выявления и устранения всех недостатков и потерь. Желательно участие и рядовых специалистов, и руководителей.
- Анализируйте весь процесс целиком. Рассматривайте не отдельные этапы, а весь путь создания ценности для клиента — от получения заказа до отгрузки готовой продукции. Иначе есть риск, что проблемы и потери просто сместятся на другие участки процесса, а общая эффективность не повысится.
- Выявите ключевую ценность для клиента. Четко определите, что именно представляет ценность для клиентов вашей продукции/услуг. Оптимизируйте процесс исключительно под создание этой ценности, исключив ненужные, лишние операции, которые только повышают себестоимость продукта.
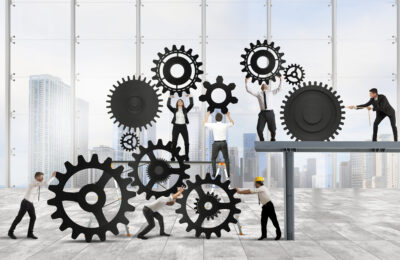
Начнем с основ: что такое производственная система?
Павел Безручко и Михаил Балакшин, «ЭКОПСИ» — о том, как оценить текущее состояние производственной системы и с чего начать ее совершенствование.
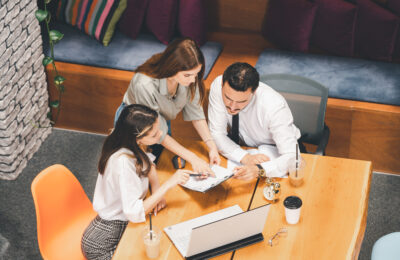
Модель ADKAR: подход к работе с персоналом в период изменений
Как добиться поддержки персоналом инициатив по улучшениям? Ответ дает модель ADKAR. В статье описываем, как инструмент помогает решить эту сложную задачу.