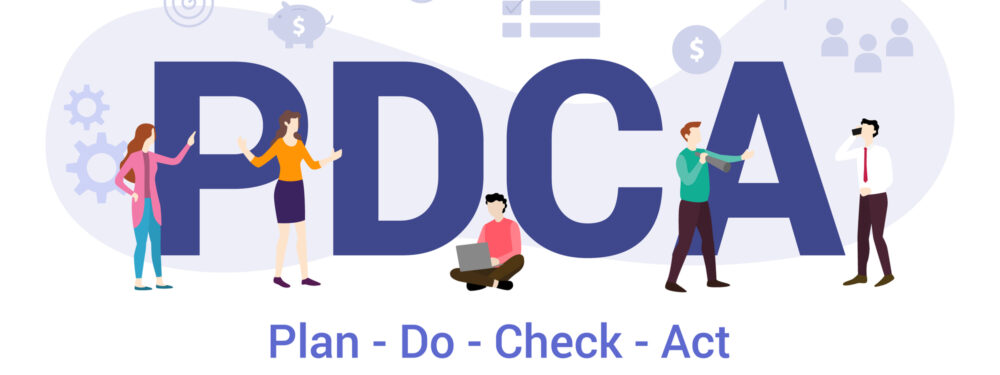
Цикл PDCA, или цикл Деминга — простой, на первый взгляд, подход для улучшения процессов — используется в бизнесе уже около 70 лет. Почему он до сих пор не потерял актуальность и остается одним из краеугольных камней бережливого производства? В статье расскажем об истории появления цикла PDCA, разберем основные фазы и выделим его ключевые преимущества. А также поговорим о том, в каких ситуациях применение цикла может быть неэффективным для бизнеса.
История появления цикла PDCA
Концепция цикла постоянного улучшения берет свое начало в трудах американского ученого и консультанта по теории управления качеством Уолтера Шухарта. Экономист отмечал, что в реальном производстве все процессы подвержены изменениям и нестабильности. Чтобы бороться с этим, он предложил три последовательных этапа контроля качества:
- Разработка технических требований и допусков на параметры продукции.
- Производство продукции в соответствии с разработанными требованиями.
- Контроль и проверка продукции на соответствие заданным параметрам.
Шухарт считал, что последовательное выполнение этих этапов позволит держать производственные процессы под контролем и обеспечит стабильность качества.
Идеи ученого сыграли революционную роль в развитии менеджмента качества, но в 1930-х годах не получили широкого распространения из-за Великой депрессии и Второй мировой войны.
В 1950-х годах теорию Шухарта развил Уильям Эдвардс Деминг. Он добавил еще один этап — «проверку» (check) и предложил использовать цикл для совершенствования бизнес-процессов в целом.
В 1950-1960-х годах Деминг популяризировал PDCA в Японии, где этот инструмент сыграл свою роль в «японском экономическом чуде». С тех пор PDCA стал классическим методом управления качеством и непрерывного совершенствования бизнес-процессов.
Фазы цикла PDCA
Что же представляет собой цикл PDCA? Это итеративный подход к улучшению процессов, продуктов или услуг, который считается одним из элементов бережливого управления. Он помогает бороться с тремя основными проблемами в бизнес-процессах:
- Потерями — действиями, которые тратят ресурсы, но не создают ценности для клиента.
- Несоответствиями — любыми отклонениями от заданного процесса, как в худшую, так и в лучшую сторону.
- Нерациональными действиями — перегрузками, хаотичной работой, отсутствием четкой системы.
Цикл PDCA состоит из четырех последовательных этапов:
P (Plan) — планирование. На этом этапе необходимо четко определить существующую проблему или возможность для улучшения, собрать и проанализировать информацию для оценки исходного состояния процесса. На основе анализа ставятся измеримые цели и разрабатываются возможные варианты решения проблемы. Определяются критерии оценки эффективности разных решений.
D (Do) — выполнение. Осуществляется реализация разработанных на предыдущем этапе решений. Важно проводить тестирование и внедрение решений сначала в ограниченных масштабах, чтобы минимизировать риски для основных процессов компании. Нужно собирать данные и измерять показатели в соответствии с поставленными целями.
C (Check) — проверка. На этом этапе проводится анализ и оценка результатов, полученных на этапе тестирования. Сравниваются фактические данные по измеренным показателям с целевыми значениями. Определяется, насколько выбранное решение оказалось эффективным, выявляются отклонения и непредвиденные проблемы.
A (Act) — действие. По результатам проведенной на предыдущем этапе проверки принимается решение — внедрять улучшение в полном объеме, провести корректировку исходного плана, вернуться на этап планирования или завершить цикл PDCA, признав проект несостоятельным. Эффективное решение стандартизируется и интегрируется в общий процесс.
После реализации улучшений формируется новое текущее состояние процесса. Затем цикл повторяется для решения следующей проблемы или задачи по оптимизации.
Преимущества цикла PDCA:
- Разбивка сложных задач на этапы. Цикл PDCA предполагает поэтапное решение проблемы — сначала планирование, затем реализация на небольшом участке, далее оценка результатов и корректировка действий. Такой подход позволяет решать сложные вопросы по частям.
- Универсальность применения. Цикл PDCA можно использовать в организациях любого масштаба и сферы — производственных, сервисных, государственных. Он эффективен как для крупного бизнеса, так и для стартапов.
- Непрерывное совершенствование. PDCA позволяет постоянно анализировать процессы в организации и находить возможности для улучшения. Циклы PDCA можно повторять многократно для постепенного продвижения к лучшим результатам.
- Управление рисками. На этапе планирования можно предусмотреть возможные риски и разработать меры реагирования. Более того, команда контролирует каждый этап изменений.
- Более быстрые результаты. Поэтапные действия и анализ позволяют быстрее получить первые результаты, скорректировать подход и повысить эффективность, минимизировав непроизводительные затраты.
- Новаторское мышление. Метод развивает у сотрудников мышление, направленное на непрерывное совершенствование бизнес-процессов.
Недостатки цикла Деминга:
- Длительность процесса. PDCA не подходит для решения срочных задач, когда требуется немедленный результат. Прохождение всех стадий занимает значительное время.
- Реактивное применение. Часто цикл PDCA используют для решения возникших проблем, а не для постоянного анализа и улучшения действующих процессов.
- Риск неверно сформулированных целей. Если цели и KPI определены некорректно, цикл PDCA может быть реализован без получения нужного результата.
Таким образом, PDCA — это отличный инструмент для вовлечения сотрудников в процесс оптимизации, структурирования и повышения эффективности улучшений. Грамотное применение цикла PDCA поможет компаниям выстроить непрерывный процесс совершенствования операционной деятельности.
О том, как цикл PDCA используют на практике, можно прочитать в статье «Оптимизация потерь с помощью технологии Costbusters».
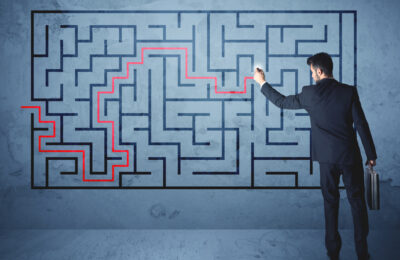
Что такое ТРИЗ: обзор методологии и инструментов
Как превратить неразрешимые противоречия в источник прорывных идей и инноваций? В материале рассказываем о методологии ТРИЗ.
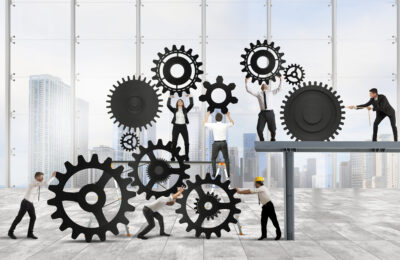
Начнем с основ: что такое производственная система?
Павел Безручко и Михаил Балакшин, «ЭКОПСИ» — о том, как оценить текущее состояние производственной системы и с чего начать ее совершенствование.