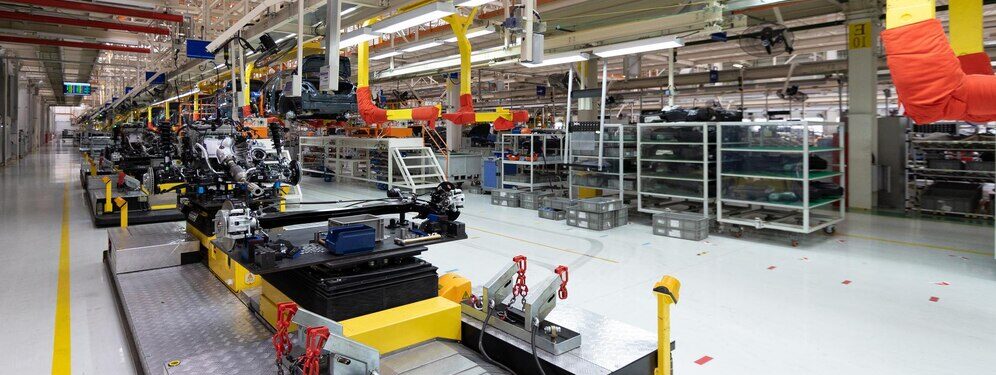
Базовые инструменты бережливого производства
В мире, где конкуренция растет, а требования к эффективности становятся все выше, компании постоянно ищут способы оптимизировать свои процессы, снизить затраты и повысить качество продукции. Все мы знакомы, а многие из нас и активно применяют для этой цели подход бережливого производства, ставший основой успеха компании Toyota. Однако всегда полезно вспомнить ключевые инструменты и принципы, которые лежат в основе этой философии. Возможно, какие-то инструменты вы еще не используете на практике, лишая себя возможности еще большей оптимизации бизнес-процессов.
Суть подхода бережливого производства
Бережливое производство (Lean Manufacturing) — это системный подход к управлению, основная цель которого — сделать больше с меньшими затратами, сохраняя при этом высокое качество продукции или услуг. Подход акцентирует внимание на улучшении процесса, в результате чего снижается количество ненужных операций и ресурсов.
Семь видов потерь в концепции бережливого подхода:
- перепроизводство;
- время простоя;
- излишние запасы;
- ненужные перемещения;
- лишние процессы;
- дефекты;
- неиспользованный потенциал сотрудников.
Базовые LEAN-инструменты
TPM (Total Productive Maintenance) — Всеобщий уход за оборудованием
Инструмент включает профилактическое обслуживание, улучшение производственных процессов и управление оборудованием на протяжении всего его жизненного цикла, чтобы минимизировать простои и продлить срок службы машин.
Внедрение и использование TPM предполагает следующие шаги:
- Обучение персонала
Важно, чтобы все понимали принципы TPM и знали, как правильно обслуживать оборудование.
- Создание команд по улучшению
Межфункциональные команды анализируют текущее состояние оборудования и предлагают меры по его улучшению.
- Регулярное обслуживание
График регулярного обслуживания и осмотров оборудования помогает избежать неожиданных поломок и простоев.
- Мониторинг и анализ данных
Сбор и оценка данных об эффективности работы оборудования позволяет выявлять проблемы и принимать меры для их устранения.
Визуальный менеджмент
Предполагает использование различных наглядных средств, чтобы обеспечить понятную и доступную информацию для всех сотрудников и эффективно управлять их деятельностью.
Основные принципы и инструменты визуального менеджмента:
- Визуальные сигналы и индикаторы
Использование ярких, легко воспринимаемых сигналов помогает идентифицировать состояние процессов. Например, светофоры могут показывать статус выполнения задач (зеленый — все хорошо, желтый — требуется внимания, красный — проблема).
- Панели и доски управления
Их использование позволяет видеть общий прогресс, быстро обнаруживать узкие места и принимать оперативные меры.
- Стандарты работы
Визуальные инструкции, стандарты и рабочие инструкции, размещенные непосредственно на рабочих местах, помогают следовать установленным процедурам.
- Графики и диаграммы
Использование графиков и диаграмм для отображения производственных данных позволяет быстро анализировать информацию и делать выводы.
Стандартные операционные процессы (SOP)
SOP — это документированные инструкции, описывающие последовательность выполнения определенных операций. Инструмент обеспечивает единообразие в выполнении задач, уменьшает количество ошибок и облегчает обучение новых сотрудников.
Практическое применение SOP включает в себя:
- Разработку SOP
Подробный анализ текущих процессов: какие действия выполняются, какие инструменты используются и какие возможны узкие места. Формулировки должны быть понятными для всех сотрудников, вне зависимости от их уровня подготовки.
- Внедрение SOP
Все работники должны быть ознакомлены с процедурами и понимать их важность. Проведите пилотное тестирование на одной или нескольких линиях. Это поможет выявить потенциальные проблемы и внести необходимые корректировки в документ.
- Поддержку и обновление SOP
SOP должны регулярно проверяться на актуальность и соответствие текущим условиям производства. Привлекайте сотрудников к обсуждению и обновлению SOP. Они могут предложить ценные улучшения, исходя из практического опыта.
«Точно-в-срок» (Just in Time)
Инструмент нацелен на минимизацию запасов и сокращение времени выполнения заказов. Продукция производится и поставляется строго в нужное время и в нужном количестве, что позволяет значительно сократить затраты на хранение и повысить эффективность работы.
Как применять JIT на практике:
- Проанализируйте текущие производственные процессы, определите узкие места, где происходят задержки или накапливаются излишние запасы.
- Разработайте гибкую и надежную систему поставок, включающую в себя оптимизацию логистики и переход на более частые, но меньшие поставки.
- Внедрение Kanban-системы поможет контролировать процесс производства и поставок в рамках JIT.
- Системы ERP и MRP могут помочь отслеживать запасы в реальном времени, управлять заказами и координировать поставки.
- Регулярные тренинги для персонала и обсуждения помогут закрепить знания и настроить команду на работу в условиях минимальных запасов.
- Используйте инструменты, такие как цикл PDCA, чтобы регулярно оценивать эффективность внедрения JIT и вносить коррективы по мере необходимости.
Картирование потока создания ценности (Value Stream Mapping)
Картирование — это метод визуализации всех этапов производственного процесса, от получения сырья до доставки готовой продукции клиенту. Основная цель этого инструмента — выявление и устранение потерь для оптимизации процессов и повышения их эффективности.
Шаги по внедрению VSM:
- Определение цели и области применения
Выявление зон, требующих улучшения — скорость выполнения, качество, сокращение затрат и т. п.
- Сбор данных
Включает в себя информацию о времени цикла, запасах на каждом этапе, времени ожидания, количестве дефектов и других показателях.
- Построение карты текущего состояния
Ключевые элементы карты: процессы, время обработки, запасы, транспортировка и другая информация, влияющая на процесс.
- Анализ карты текущего состояния
Определите узкие места, которые замедляют процесс, и области, где затрачивается больше ресурсов, чем необходимо.
- Построение карты будущего состояния
Здесь должны быть определены ключевые изменения, которые необходимо внедрить.
- Разработка плана действий и внедрение изменений
План должен включать сроки, ответственных лиц и ресурсы, необходимые для выполнения изменений.
- Мониторинг и постоянное улучшение
Используйте VSM для повторного анализа процесса через определенные промежутки времени, чтобы убедиться, что изменения приводят к ожидаемым результатам.
Встроенное качество (Built-in Quality)
Концепция встроенного качества предполагает, что контроль качества встроен в каждый этап производственного процесса. Основные принципы встроенного качества:
- Превентивное предотвращение ошибок
Например, использование шаблонов или инструментов, которые физически не позволят собрать деталь неправильно.
- Непрерывное обучение и улучшение
Регулярные встречи и обсуждения позволят выявлять и устранять узкие места в процессе. Важно также обеспечить регулярное обучение работников новым принципам и методам.
- Использование статистического контроля
Сбор и анализ данных о вариациях в рабочем процессе может помочь идентифицировать и устранить причины отклонений до того, как они перерастут в серьезные проблемы.
- Встроенные системы для обеспечения качества
На этапе проектирования продукта учитываются все возможные сценарии использования, чтобы минимизировать риски возникновения дефектов в дальнейшем.
- Автономизация
Внедрение систем с функцией автономизации позволяет снизить человеческий фактор и улучшить контроль над процессами.
Организация рабочих мест по системе 5S
5S — это методика организации рабочего пространства, которая помогает создать безопасную и эффективную рабочую среду, минимизируя потери времени и ресурсов.
Внедрение 5S состоит из пяти этапов, каждый из которых направлен на улучшение конкретного аспекта организации рабочего пространства.
- Сортировка
Проведение инвентаризации рабочего места. Например, на производственной линии отсеиваются инструменты, которые не используются ежедневно.
- Систематизация
Создание четкой системы хранения инструментов и материалов, например, с использованием маркировки и цветовых кодов.
- Содержание в чистоте
Ежедневная уборка сотрудниками рабочих мест, включая осмотры оборудования и инструментов.
- Стандартизация
Создание стандартов, таких как контрольные списки для проверок или визуальные инструкции, помогает закрепить внедренные практики.
- Совершенствование
Регулярное обучение и мотивация сотрудников участвовать в улучшении рабочего места.
Кайдзен
Кайдзен — это философия постоянного улучшения, которая поощряет сотрудников на всех уровнях вносить предложения по улучшению рабочих процессов.
Практическое применение кайдзен включает в себя:
- Внедрение кайдзен в производственных линиях;
- Предложение идей сотрудниками;
- Создание малых групп для решения конкретных проблем;
- Регулярные встречи и обсуждения;
- Использование инструментов визуализации;
- Тренинги по кайдзен;
- Признание и поощрение сотрудников за предложения и внедрение улучшений.
Канбан
Канбан — это система управления производством, которая использует визуальные сигналы (например, карточки) для контроля потока материалов и производства. Этот инструмент помогает поддерживать баланс между спросом и предложением, минимизировать запасы и сократить время ожидания.
Примеры практического применения:
- Создание канбан-досок
Например, каждая стадия рабочего процесса может быть представлена на доске отдельными колонками, а задачи — карточками, которые перемещаются по мере выполнения работы.
- Системы канбан для управления запасами
В производстве можно использовать систему двоичных контейнеров, где один контейнер с компонентами используется в производстве, а второй — в резерве.
- Пул-система
Канбан обеспечивает систему вытягивания, где производство новых изделий начинается только по мере появления спроса от следующего этапа производства или потребителя.
- Балансировка рабочей нагрузки
Используя канбан, можно распределять задачи таким образом, чтобы избежать перегрузок у отдельных работников или команд.
Внедрение бережливого производства требует времени и усилий, но результаты того стоят: повышение эффективности, удовлетворенность клиентов и сотрудников, а также устойчивое развитие бизнеса.
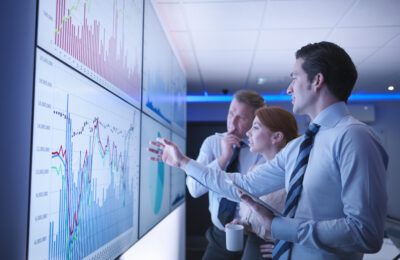
Цифровизация и автоматизация — путь к операционной трансформации
Современные цифровые технологии преобразуют бизнес, снижая издержки и повышая эффективность. Узнайте, как ERP, BI, RPA и AI помогают компаниям управлять операционной трансформацией, создавая условия для устойчивого роста и конкурентного преимущества.

Как Севергрупп растит проектных менеджеров: опыт, который работает
Михаил Куликов, Севергрупп — о том, как компании удалось повысить долю перспективных сотрудников практически втрое.