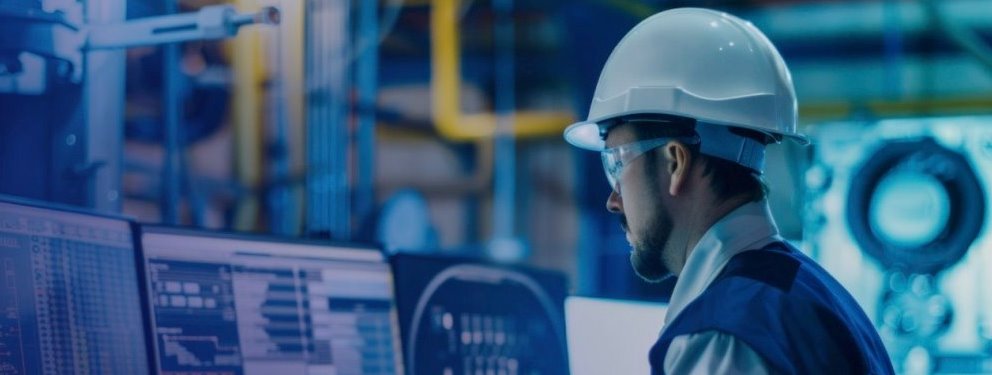
Визуализация и анализ производственных данных: кейс ЕвроХима
За полтора года использования инструмента ИнсЭф на предприятиях ЕвроХима экономический эффект от реализованных мероприятий и согласованных новых проектов превысил 1 миллиард рублей. Что это за решение, как оно помогает работать с производственными данными и менять культуру команды, Клубу ЭБС рассказал Даниил Якимец, начальник управления по операционным улучшениям АИМ-менеджмент.
Предпосылки проекта
ЕвроХим активно внедряет решения на своих промышленных площадках в рамках цифровизации технологического процесса. В основе этих решений – передовые технологии искусственного интеллекта, моделирования, видеоаналитики и промышленного интернета вещей. Усольский калийный комбинат – первое предприятие, где ЕвроХим отработал комплексный подход к цифровизации. Компания рассматривает цифровизацию как долгосрочный тренд и инструмент для повышения безопасности, эффективности и оптимизации производственных процессов.
Комплексная цифровизация химического производства представляет собой системный подход к управлению, который охватывает все этапы производственного процесса – от отдельного узла до цеха и всего предприятия в целом. Такой интегрированный метод позволяет не только оптимизировать отдельные операции, но и обеспечить слаженную работу всей производственной цепочки в части эффективности и безопасности.
Полтора года назад в компании приняли решение создать собственный инструмент для визуализации и анализа производственных данных. Что к этому подтолкнуло? Во-первых, аналогичные решения успешно работают у других компаний. Во-вторых, не секрет, что существует устойчивый тренд на цифровизацию и работу с большими данными. Чтобы развиваться и оставаться конкурентоспособными важно этот тренд учитывать.
Руководство поддержало инициативу, потому что увидело в ней конкретную экономическую выгоду. Так ИнсЭф стал одним из ключевых проектов программы компании по повышению операционной эффективности.
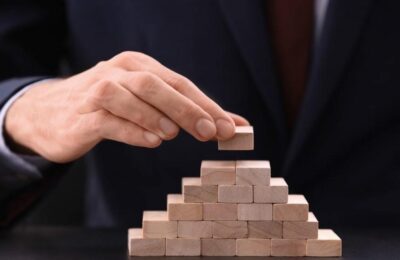
Четыре столпа операционного совершенства
Интегрированный подход к операционному совершенству обеспечивает основу для непрерывного улучшения и трансформации бизнеса.
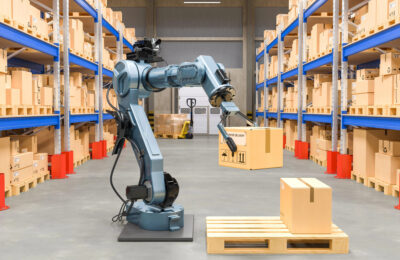
Будущее логистики: как автоматизация меняет складские процессы
Автоматизация логистики и складских процессов — о ключевых трендах, таких как роботизация, внедрение автономного транспорта и цифровизация, которые помогают компаниям снизить издержки, повысить эффективность и способствуют экологически чистому будущему в логистике.